The Ultimate Guide to Choosing the Right Packaging Machine Repair Experts
The Ultimate Guide to Choosing the Right Packaging Machine Repair Experts
Blog Article
The Ultimate Overview to Product Packaging Machine Fixing: Maintain Your Workflow Running Smoothly
Recognizing the intricacies of product packaging device fixing is critical for keeping ideal performance and lessening disturbances. Routine maintenance not just expands the life of these makers however likewise addresses typical concerns that can restrain performance.
Importance of Regular Upkeep
Normal upkeep of product packaging machines is vital for making sure optimal efficiency and longevity. By executing a structured maintenance routine, operators can recognize possible concerns before they rise into substantial troubles. This proactive approach not only decreases downtime yet likewise expands the life expectancy of the devices, inevitably bring about minimized operational prices.
Regular examinations enable the evaluation of critical elements such as sensing units, belts, and seals. Resolving damage immediately prevents unanticipated failures that could disrupt production and lead to expensive fixings. In addition, regular upkeep assists make certain conformity with sector criteria and laws, promoting a secure functioning atmosphere.
Furthermore, maintenance activities such as cleansing, calibration, and lubrication significantly enhance equipment performance. Boosted performance translates to consistent item high quality, which is essential for maintaining client complete satisfaction and brand name credibility. A well-kept packaging equipment operates at ideal speeds and minimizes material waste, adding to overall efficiency.
Common Packaging Equipment Problems
Packaging devices, like any intricate machinery, can encounter a variety of typical concerns that might prevent their performance and efficiency - packaging machine repair. One prevalent problem is inconsistent sealing, which can cause product perishing and waste if packages are not correctly sealed. This frequently results from misaligned elements or used securing components
One more regular concern is mechanical jams, which can happen because of foreign items, used components, or improper placement. Jams can trigger hold-ups in production and rise downtime, ultimately impacting overall performance. Furthermore, digital malfunctions, such as failing in sensing units or control systems, can interrupt procedures and lead to incorrect dimensions or irregular machine behavior.
Furthermore, problems with item feed can also arise, where products may not be provided to the packaging location continually, creating interruptions. Finally, wear and tear on rollers and belts can bring about suboptimal efficiency, calling for instant interest to avoid additional damages.
Understanding these typical issues is essential for maintaining the integrity of packaging operations, ensuring that machinery runs smoothly and efficiently, which consequently aids in conference production targets and keeping item high quality.
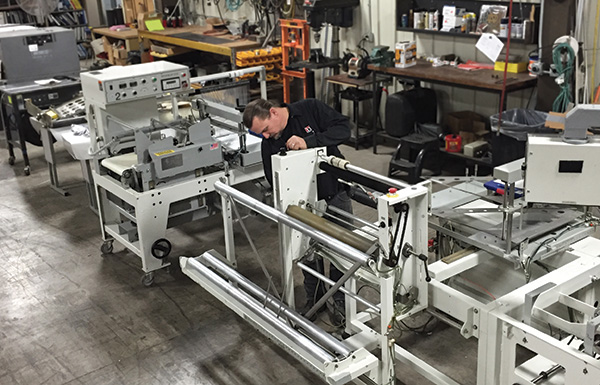
Troubleshooting Methods
Efficient repairing methods are important for promptly addressing issues that occur with product packaging machines. An organized method is crucial for recognizing the origin of malfunctions and reducing downtime. Begin by gathering info regarding the signs and symptoms observed; this may consist of uncommon noises, operational delays, or try these out error codes shown on the maker's interface.
Following, refer to the device's guidebook for troubleshooting guidelines particular to the model concerned. This source can give valuable understandings right into usual issues and advised analysis steps. Make use of aesthetic assessments to look for loosened connections, worn belts, or misaligned components, as these physical variables frequently contribute to functional failings.
Apply a process of removal by testing individual maker functions. For example, if a seal is not forming correctly, examine the company website sealing mechanism and temperature level setups to establish if they satisfy operational specifications. Document each step taken and the outcomes observed, as this can help in future troubleshooting initiatives.
Fixing vs. Substitute Decisions
When faced with equipment breakdowns, determining whether to change a packaging or fix maker can be a facility and essential selection. This choice depends upon a number of crucial aspects, including the age of the device, the extent of the damages, and the projected influence on operational effectiveness.
First of all, take into consideration the equipment's age. Older machines may need more regular repair services, causing greater collective prices that can exceed the investment in a new system. Furthermore, examine the intensity of the breakdown. Small concerns can commonly be solved promptly and economically, whereas considerable damages could demand a significant financial commitment for repair work.
Functional downtime is an additional critical consideration. Investing in a new machine that offers boosted efficiency and dependability might be more prudent if repairing the maker will trigger extended delays. Think about the accessibility of components; if substitute components are difficult to come by, it may be more calculated to change the machine totally.
Inevitably, carrying out a cost-benefit evaluation that consists of both lasting and instant implications will certainly aid in making an educated decision that lines up with your functional objectives and budgetary constraints. (packaging machine repair)
Safety Nets for Longevity

Secret preventive procedures include routine lubrication of moving components, alignment checks, and calibration of sensors and controls. Establishing a cleansing routine to eliminate particles and pollutants from machinery can significantly minimize deterioration (packaging machine repair). In addition, keeping track of functional parameters such as temperature and resonance can help spot abnormalities early
Training team to identify indicators of wear or malfunction is an additional vital element of preventive maintenance. Encouraging operators with the knowledge to perform basic troubleshooting can cause quicker resolutions and decrease operational disturbances.
Documentation of upkeep tasks, consisting of solution records and assessment findings, cultivates accountability and promotes informed decision-making relating to substitutes and repairs. By prioritizing preventative actions, services can guarantee their packaging equipments run at peak efficiency, eventually causing increased efficiency and lowered functional costs.
Conclusion
In conclusion, the efficient maintenance and repair of product packaging machines are critical for sustaining functional effectiveness. By applying preventative procedures, services can enhance device longevity and guarantee continuous productivity in packaging operations.
Comprehending the complexities of product packaging device repair work is essential for maintaining optimal performance and reducing disturbances.Routine upkeep of packaging devices is important for ensuring ideal performance and long life.Product packaging machines, like any type of complicated equipment, can experience a variety of common issues that may hinder their performance and performance. If repairing the maker will certainly trigger prolonged delays, investing in a brand-new equipment that supplies boosted effectiveness and reliability may be a lot more prudent.In final thought, the effective upkeep and fixing of packaging makers are vital for sustaining functional efficiency.
Report this page